Oceanic Plaza
Certifications & Awards
Project Team
- LEED/Re-commissioning Consultant: MMM Group
- Owner: Oxford Properties
Green Building Audio
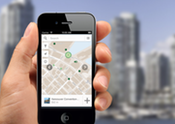
Our audio tours qualify.
Get one today!
Derek Page & Steve Partrick, Oxford Properties and Juan Monterrosa, MMM Group
Summary
Oxford Properties’ Oceanic Plaza is a 403,000 sq/ft office building located at 1066 West Hastings Street in Vancouver, BC. Built in 1977 and renovated in 2005, the building has 26 floors providing office space to 1100 building occupants. In addition to its central location, tenant amenities and spectacular views of the Burrard Inlet and North Shore mountains, Oceanic Plaza is pursuing excellence in energy efficiency. The project is seeking certification through the LEED Existing Building: Operations and Maintenance (EB:O&M) program, implementing myriad comprehensive improvements with measurable benefits.
Sustainable Sites
Centrally located in Coal Harbour in downtown Vancouver, Oceanic Plaza
is in close proximity to the Skytrain subway station and major transit
lines on Burrard and Hastings Street.
The Oceanic Plaza shares amenities space with Oxford Properties’ adjacent Marine Building and Guinness Tower, for access to secure bike storage, showers, lockers and a fitness facility for the support of healthy, active lifestyle which includes alternative transportation to and from work.
The central location and provision of infrastructure for alternative transportation fosters a culture of low-emission travel. A sample survey showed that 77% of occupants use some form of alternative transportation to travel to and from work rather than a single occupancy vehicle.
Water Use Reduction
A water audit was completed as part of the LEED investigation phase to find areas where the building was over-using water. Operations implemented the changes to reduce overall water consumption by over 10%.
Specifically, lavatory aerators reduced water flow rates from up to 10.8 Litres per minute (Lpm) in some cases to 1.9 Lpm. Water closet flush rates were reduced from 9.3 Litres per flush (Lpf) to 7.6 Lpf
Energy
Investment in energy conservation measures can reduce overall energy consumption, but how does a building determine where to focus these investments for the greatest impact? Where are the greatest savings? To answer these questions, facilities must first undertake an investigation and analysis.
Oxford Properties enlisted Oceanic Plaza, as well as their nearby Marine Building, Guinness Tower and 401 West Georgia, into the Continuous Optimization for Commercial Buildings Program (C.Op.), offered by BC Hydro Power Smart in partnership with Fortis BC. The program was set up to assist commercial building owners identify and take corrective action on energy wasting operational systems and continuously monitor building performance for ongoing maintenance and improvement of energy efficiency, which reduce operating costs.
Eligible customers such as Oxford Properties received funding towards the cost of re-commissioning services to study their buildings and recommend energy efficiency improvements, as well as access to an energy management information system (EMIS) to assist in tracking their building’s performance after the re-commissioning work was complete. In return, program participants agree to implement, at their cost, measures identified by the re-commissioning study that have a payback of two years or less.
MMM Group Ltd. conducted the retro-commissioning investigation as part of the program, in addition to supporting Oxford Properties through the process for LEED EBOM certification.
The retro-commissioning investigation identified deficiencies and improvements in the operation of a facility’s mechanical equipment, lighting, and related controls. Opportunities for corrective action were identified that could reduce energy consumption and preserve or improve indoor environmental quality.
The investigation focused on low-cost improvements with short paybacks, although major capital improvement opportunities were also identified. Major retrofit measures were beyond the scope of the Program but other BC Hydro programs provide a variety of incentives to complete the retrofits. Two retrofits, VFD on the chilled water pump and VFD on chiller compressor, were identified as a part of this investigation that could potentially qualify for other BC Hydro Power Smart programs.
For each of the measures recommended below, costs, payback calculations and incentive amounts were provided to the client:
Optimization of Sequence of Operation on BAS
The controls contractor produced the last sequence of operations in 2010. It was an incomplete sequence of operation for the building system, which was notably missing a sequence for the heating system as well as for a combined sequence of operation provided by another contractor, which should have also included the Multistack Heat Recovery Chiller.
The sequence of operation were reviewed and updated. New additional optimized sequences were recommended through an in-depth review process. Once all control sequences were reviewed and optimized, the control drawings were updated to serve as As-Builts.
Compartment Fans Operating Too Early
It was discovered that the compartment fan units were operating as early as 5:15 am on weekdays, whereas most Oceanic Plaza occupants do not arrive until 7 or 8 am. Updating the Direct Digital Controls (DDC) to schedule the fans starting up later was an easy measure for the project to implement immediately.
Constant Temperature Heating System Enabled Setpoint Change
The constant temperature heating system at Oceanic Plaza was enabled once outdoor air temperature was <15 ̊C. Based on the utility bill analysis performed for the building, it was discovered that the balance temperature is around 12-13 ̊C. Reprogramming the BAS to enable the heating system once outdoor air temperature is at less than 12 ̊C means that the building’s heating won’t kick in any earlier than needed, thereby creating energy savings.
Constant Temperature Heating System Setpoint Change
The original heating system setpoint was at 80 ̊C. MMM Group recognized that this was too high. Building operators on their own accord adjusted the setpoint down to 60 ̊C for additional energy savings. Building operators also adjusted the steam valve schedules to turn off at 6 pm, rather than its original constant operation.
Chilled Water Reset Strategy
The chilled water setpoint for the chiller was set at 12 ̊C. Implementing a chilled water reset strategy results in lower chilled water supplied to the cooling coils of the compartment floors fans. This cooler chilled water cools tenant space supply air more than if the CHWS temperature was set at 12 ̊C. Cooler supply air makes the VAV boxes minimize their damper position, which results in a lower overall airflow supplied to the tenant spaces. The energy savings are from the variable speed drive reduction in the compartment fan motor speed in response to the tenant spaces requiring overall less airflow.
Condenser Water Reset Strategy
The entering condenser water temperature setpoint used to be manually adjusted on the Building Automation System. Creating a setpoint based on wet bulb temperature and estimated cooling tower approach, either using an installed wet bulb temperature sensor or via the Natural Resources Canada website.
Clean Intake Louvers and Fan Housing
Dirty louvers restrict outside airflow drawing in. Likewise, dirty fan housing can cause maintenance issues for the fan and potential IAQ issues. Oxford facilities management cleaned these louvers and housing for immediate and low-cost benefits.
Faulty Pneumatic Actuator for Fresh Air Damper
A faulty actuator on 12th floor needed to be replaced in order to properly balance the fresh air floor to the compartment fan room.
VFDs
Major retrofit measures were beyond the scope of the BC Hydro Continuous Optimization Program, but other BC Hydro programs provide a variety of incentives to retrofit Variable Frequency Drives (VFDs). A VFD, or variable speed drive, installed on a motor can reduce its runtime, creating efficiencies and equipment longevity. Any application that doesn’t need to be running at full speed can be controlled with a VFD to allow the speed of the motor-driven equipment to match the load requirement, which cuts down on energy use and costs. The following measures, were recommended:
VFD on Chilled Water Supply Pump
The chilled water supply pump was operating at constant speed. A VFD with differential pressure sensors, with a minimum flow on the chillers cuts down on pump runtime, creating energy savings.
VFD on Chiller Compressor
The chiller was operating based on its capacity control, whereas a variable speed drive optimizes its operation when there is a minimum flow set on the chiller.
In the interest of continuous optimization, the following measures were recommended for future implementation and are being considered for future budgets:
Install Exhaust Air Damper in Penthouse Mechanical Room
Due to temperature differentials during unoccupied periods, the stack effect created heat loss from the exhaust air grille in the Penthouse Mechanical Room due to a non-existent damper.
Compartment Fan Motors are Oversized and Operating Above the Fan Curve
Compartment fans currently deliver 18,000 cubic feet per meter of airflow each, rotating at 1,076 RPM. Research on a similar fan type showed that the fan only needed an RPM value between 530 RPM to 654 RPM to deliver 18,000 CFM. Replacing the motor to a smaller size (15HP) would create a more efficient system that would save energy.
Additional measures to be considered in future retrofits include:
-Replacement of Shell and Tube Heat Exchanger to More Efficient Heat
Exchanger (Capable of Recovering Latent Heat)
-Install Photocells to Control Outdoor Lighting
-Convert Constant Volume Make-Up Air Unit to a VAV System Equipped with
CO2 Sensor for Demand Control Ventilation
Energy Star rating
To determine how Oceanic Plaza fared among other projects in Canada,
its energy data was entered into the Energy Star Portfolio Manager to
generate an efficiency ratio. This ratio is computed using actual and
predicted source energy use intensity, and is compared to national
distribution to assign a score. Buildings with an Energy Star score of
75 or higher are among the top 25% percentile of similar performing
buildings. Oceanic Plaza scored an efficiency ratio of 68.
Indoor Environmental Quality
ASHRAE and I-BEAM
To optimize the amount of fresh outdoor air (OA) provided to interior spaces, air handling equipment was calibrated to provide OA levels compliant with ASHRAE 62.1-2007 standards; high quality filtration was installed to reduce contamination. As a means to ensure optimal indoor air quality, the building manager follows I BEAM (Indoor Air Quality Building Education and Assessment Model) protocols. Created by the U.S. Environmental Protection Agency (EPA), this comprehensive tool helps identify issues and improve air quality.
The education and assessment model provides outlines how sources of pollution, heat and humidity, combine with mechanical systems to affect indoor air quality. Learning to manage and control these factors equips building operators with the tools to address air quality for occupant comfort, health and performance.
Facilities management conducts regular indoor air quality inspections and identifies ways to reduce occupant exposure to odours and contaminants.
Cooling tower management
The Oceanic Plaza uses water-cooled air as an air conditioning system.
Known as cooling towers, these systems require careful maintenance to
prevent adverse occupant health effects from microbial growth. A cooling
tower management plan was created for training and maintenance purposes
around chemical treatment, bleed-off, and biological control. A
conductivity meter was installed to improve water efficiency and adjust
the chemical rate and maintain proper concentration. The sum of these
activities ensure the system runs safely and efficiently.
Policies
Policies create the structure needed for change implementation. This is the key point where resource efficiencies, and occupant health benefits move from best practice to standard practice. Multiple policies were developed and implemented for Oceanic Plaza including:
-A comprehensive waste management program to encourage diversion of materials from the landfill, including paper, cardboard, electronics, toner, batteries and furniture by either recycling or donation programs
-Low impact pest control to use humane and chemical free methods of pest control
-Building Exterior and Hardscape Management Plan to ensure snow removal, maintenance equipment use, exterior cleaning, painting and sealing work are low-impact, with as little associated noise, emissions, soil compaction, water contamination, and vegetation impact as possible.
-A purchasing policy to procure sustainably sourced paper products, office supplies, returnable toner cartridges, and rechargeable or low-heavy metal content batteries.
-Lightbulbs and lamps have also been regulated so as to have a maximum of 90 picograms per lumen hour of mercury.
-Low impact cleaning to promote the use of low-concentrate chemicals that are better for occupant health and extend life of building surfaces.
Tenant Engagement
Some of the most positive impacts in a building’s operations can stem from its tenants and operational policies.
To harness the energy of change leaders, a Green Team meets quarterly to focus on energy, water and resource use reduction and promoting participation in ongoing programs.
Installations in the lobby and elevator inform occupants about aspects of sustainability, pertaining to the building and beyond, as well as programs and events.
What building owners can do
There are a number of steps that building operators can take to improve the environmental performance of their buildings.
Building operators and facilities managers can engage in similar forms
of measurement and benchmarking to examine effective strategies for
change in infrastructure and operations. Signing up and using the Energy
Star Portfolio Manager is an easy way to get started. A training section
is available on their website as well as a starter kit on how to
benchmark.
www.energystar.gov/buildings/training
www.energystar.gov/buildings/facility-owners-and-managers/existing-buildings/use-portfolio-manager/get-started-benchmarking
Participation with local chamber of commerce green teams, local environmental initiatives and community challenges can help extend a project’s impact of sphere of influence beyond the building.
For building owners who recognize the long-term financial value of a green retrofit, gathering data is key. Anthony Esposti, Senior Manager of Corporate Financing at Business Development Bank of Canada says energy-saving fixtures usually pay for themselves within two to six years. In order to ensure that retrofits actually deliver those savings, building owners need the following pieces of information:
• Baseline data on the building’s energy and water use before the
retrofit;
• Recommendations on equipment to reduce baseline use;
• Projected energy reductions and cost savings, as estimated by an
engineer
• A means to collect and monitor data on the building’s energy and
water use after the retrofit
A number of consulting companies provide this type of service, but financing for existing buildings can provide a challenge to pay for these services with the recommended equipment upgrades.
Esposti advises landlords to inquire about retrofit financing options with their current lenders. Using information on the benefits of green buildings from sources like the Canada Green Building Council and Natural Resources Canada may aid in a loan request.
BDC is currently looking into ways to assist entrepreneurs reduce their companies’ greenhouse gas emissions and increase energy efficiency. Esposti also urges building owners to contact Business Development Bank of Canada with regard to financing as they “do have money available for doing things aside from mortgage financing.”
What home owners can do
Homeowners can also engage in improving home performance through similar benchmarking processes
The Energy Star Home Advisor program allows homeowners to create a profile, provide utility bills to create a baseline and then receive tailored recommendations to adopt. www.energystar.gov/campaign/assessYourHome
One effective way to determine a base level of home energy performance is to book an assessment with a Certified Energy Advisor (CEA). CEA’s conduct an air-leakage test to produce an energy efficiency rating or Energuide rating, which is a score out of 100. Energy reduction measures are implemented, such as air sealing, insulation and HVAC system upgrades, to improve performance and Energuide rating. www.nrcan.gc.ca/energy/efficiency/housing/new-homes/5035
Some financial and public institutions provide loans, construction grants, subsidies, tax rebates or other incentives for energy upgrades. City Green Solutions, a social enterprise that delivers energy efficiency services, has provided a Searchable Incentive Database for British Columbians: www.citygreen.ca/incentives.
Renters can improve home energy performance with quick projects, such as plugging electronics into a powerstrip to have a convenient ‘turn-on/turn-off’ point and replacing air filtration on HVAC systems. A list of resources are available on the Energy Star website
Sources: US EPA, Energy Star, CaGBC, City Green Solutions, MMM Group, Oxford Properties, Business Development Bank of Canada